



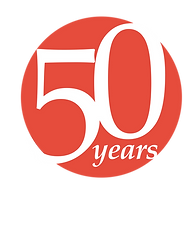
Conspar assists with the building maintenance needs of many Perth properties that are strata managed.
Working closely with strata managers and the companies they represent, Conspar stands out from the crowd in terms of offering the most cost-effective solutions to building problems without compromising on expertise and service delivery since it began operating in 1969.
Whether it be detecting a long-standing water ingress problem to treating the resultant concrete cancer or waterproofing balconies to preventative maintenance installation of protective coatings, Conspar can assist.
If more than one area of repairs is required, Conspar can also assist from roofwork, brickwork, plumbing and window work to carpentry, tiling and painting.
Helping to protect Perth’s heritage buildings
Address cracking of brickwork on building facade.
Address cracking of brickwork on building facade.
PROJECT TEAM
PROJECT TEAM
SERVICES OVERVIEW
PROJECT TEAM
Carry out concrete cancer treatment of structural concrete columns and leading edges of carport.
Address concrete cancer at carport underneath balcony.
Carry out concrete cancer treatment of structural concrete columns and leading edges of carport.
Address concrete cancer at carport underneath balcony.
Address concrete cancer at carport underneath balcony.




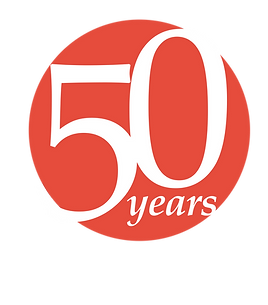
Led by two registered builders, Conspar provides building defect reports and is able to carry out the repairs for you.
All work is carried out to Australian Standards and based on 50 years' experience in the building industry.
Led by two registered builders, Conspar provides building defect reports and is able to carry out the repairs for you.
All work is carried out to Australian Standards and based on 50 years' experience in the building industry.
Led by two registered builders, Conspar provides building defect reports and is able to carry out the repairs for you.
All work is carried out to Australian Standards and based on 50 years' experience in the building industry.
Led by two registered builders, Conspar provides building defect reports and is able to carry out the repairs for you.
All work is carried out to Australian Standards and based on 50 years' experience in the building industry.
PROJECT TEAM
PROJECT TEAM
PHONE
OFFICE
Protecting Concrete
WHY IT IS IMPORTANT TO PROTECT CONCRETE ELEMENTS FROM MOISTURE AND CHEMICAL ATTACK
PROTECTION OF CONCRETE ELEMENTS
Where concrete surfaces have become porous and fine cracks (or 'crazing') have developed, water and other contaminates can penetrate through to the structural substrate and reinforcing steel and allow concrete cancer to develop. Often the shear quantity of these cracks make individual repair too costly or result in an unsightly result. In these cases we recommend covering the surfaces with our waterproof coatings (more information here) in order to protect the entire surface from further moisture ingress and reduce the onset of concrete cancer. The coating is able to safely bridge fine cracks and crazing present due to being thick and flexible, and can be embedded with fibreglass matting in order to reinforce it and provide an anti-slip surface.
Weathered surfaces also present high-risk slipping hazards in high traffic, common access areas or on industrial / warehouse floors, and present associated liability issues (for residents / workers and visitors).
Failure of control joints, movement joints and / or expansion joints also allow water to penetrate into the substrate. Furthermore, simple 'cold-formed' control joints do not offer the correct allowance for movement that results from thermal expansion and contraction of the structure. This can lead to fracturing of concrete elements immediately adjacent to these areas and create further areas for water penetration.
Typical of buildings constructed in the 1950's and 1960's in Perth, Western Australia, the location of steel reinforcement within concrete elements may be too close to the surface. Inadequate concrete coverage around steel reinforcing enables any water that permeates into the concrete to easily access the steel causing it to rust.
Moisture staining typically on landings and walkways indicates insufficient drainage of water from these areas. This accelerates the deterioration and ageing of applied coatings / surface treatments, exposing the concrete below to moisture penetration. Furthermore, ponding water has a longer duration to penetrate the surface of the concrete.
RECOMMENDATIONS
a. Apply protective coating systems to surfaces following correct surface preparation, selected for site specific functional characteristics required. Characteristics to be considered may include warranty duration (Conspar can uniquely provide 10, 15 and 20 year warranty options), whether waterproof coatings with anti-slip properties are required, and whether the elements will be exposed to chemical attack.
b. Repair / reinstate / re-level concrete toppings following concrete cancer repairs (if required).